Traction applications refer to the general term for capacitors used in trains or "railway vehicles." Electric propulsion systems and electrical systems that support brakes, lighting and power supplies are the focus areas for such applications.
In order to achieve smooth acceleration and deceleration, it is necessary to properly control the power supply of the train motor. At present, the most common method is to use an inverter, that is, a power electronic circuit that turns on or off current in a thousandth of a second or less. By changing the on/off time of the switches in the inverter, the inverter can easily control the power supply to the train motor. For example, 100% turn-on time means maximum power, and 50% turn-on time means half of power. The advantage of using an inverter is that the train engineer can control the power required to drive the train without generating a lot of heat – a common problem with conventional systems, which require the use of a resistor box to keep the motor unused. Electricity is converted into heat and then emitted.
One of the challenges faced by inverter R&D engineers is that long power lines (such as overhead contact lines in regional train systems) cannot solve the problem of rapid current changes flowing through them, and the inverter can do just that. The purpose of controlling the power supply to the motor is achieved. The solution to this problem is to use a capacitor to store the current. According to this scheme, if the inverter turns off the current, all current flows into the capacitor . If the inverter turns on current, the current is supplied by the power line and capacitor. With a properly sized capacitor, the current in the power line is the average current that the motor needs at the time, and the current does not change very quickly. The current in the capacitor is the difference between the slowly varying average current and the on/off current caused by the inverter. This is also known as "ripple current."
Capacitor products come in a variety of ways and each has its own advantages and disadvantages. For traction applications , the capacitor is based primarily on plastic film or aluminum electrolysis processes. Plastic film capacitors generate almost no heat due to ripple current, and their characteristics rarely change with time, and can reach the manufacturing level that can withstand 20kV power line voltage. For power line voltages up to 1.2kV, aluminum electrolytic capacitors can store the same amount of current in a smaller package and at a lower cost than plastic mold capacitors. However, aluminum electrolytic capacitors generate heat due to ripple current and have a limited lifetime (depending on temperature), resulting in a more versatile design-in process. This article describes all aspects of the aluminum electrolytic capacitor design integration process and the ideal features that a capacitor product for this application should have.
Choose the best capacitor for each application
Aluminum electrolytic capacitors are used in two main traction applications :
Used as a DC link capacitor in a traction drive to control the speed of large motors
Used as a DC link capacitor in an auxiliary power supply for railway vehicles, for example for air conditioning
In both applications, the aluminum capacitor acts as an energy buffer to ensure stable operation of the switch mode inverter or auxiliary power circuit that drives the motor. The aluminum capacitor can also act as a filter to prevent high frequency components from the switch mode inverter from interfering with the grid.
The key selection criterion for aluminum capacitors is the required ripple current, which corresponds to the 8kHz - 20kHz high frequency ripple current generated by the inverter.
To maximize operating life, the aluminum capacitor should be located as low as possible. Forced cooling or mounting capacitors on the heat sink can increase component life, especially when combined with an extended cathode structure inside an aluminum capacitor.
It is wise to specify minimum capacitance requirements to ensure stable operation of the drive. Low inductance (ESL) also helps filter switching noise. For screw terminal devices with large housing sizes, ESL values ​​below 13nH can be achieved.
Aluminum capacitors are often used in series and in parallel because the voltage in a railway vehicle can be as high as 1,200V. In these cases, three aluminum capacitors can be used in series. At the same time, care should be taken to balance the intermediate voltage between the capacitors, for which a so-called leakage resistor is usually used.
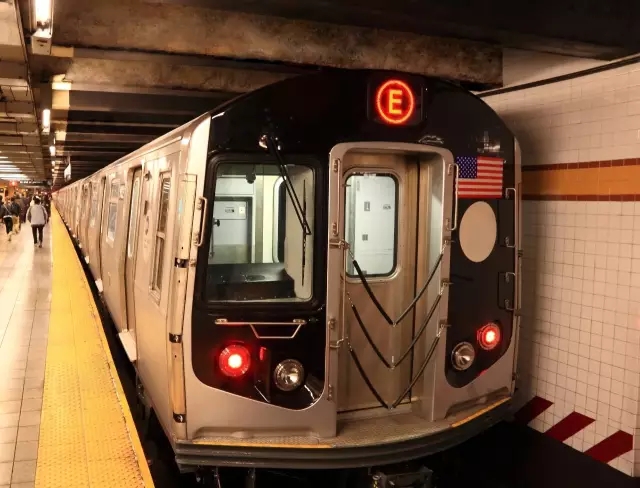
Ideal for capacitive solutions
The ideal capacitor for this application is Vishay's 110 PHT-ST series. This family of capacitors is designed for traction applications and offers high ripple current and long life. Vishay has a long history of developing screw terminals, dating back to 1988, and the brand name used in advance is Philips.
Typical examples on the traction market are:

The series has been approved for OEM applications and as a replacement for drives on existing railway vehicles from German manufacturers (AEG), Alstom, General Electric and Siemens.
In retrofitting projects, achieving mechanical interchangeability and providing engineering support for selecting the best alternatives is a key feature in deciding not to work with OEM suppliers. Vishay offers tailor-made products based on customer needs, operating temperatures ranging from 85°C to 105°C and 2,000 hours to 15,000 hours at maximum temperatures. The 100,000 hour service life at 70 ° C is another standard that can be achieved with Vishay's professional components. In addition, we can provide a life calculation method to support the performance promise of the capacitor for a specified service life in a specific application. We offer metric M5-8mm to M6-18mm and US threaded 1â„4-28 UNF terminals. Capacitor products are delivered with screws and washers.
3-phase IGBT power stage
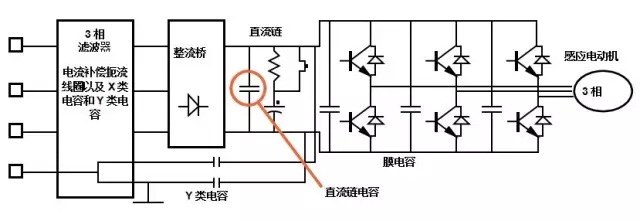
Inverter typical block diagram
Long Range Fiberglass Horn Speaker
Long-range glass fiber reinforced plastic Horn Speaker, the box is made of glass fiber and anti-aging agent, durable, beautiful and environmentally friendly, built-in network decoding module, stereo power amplifier, high-fidelity speaker
Remote FRP horn-type integrated network audio decoding speaker, used for audio decoding and sound restoration in broadcast partitions, especially suitable for open-air environments, such as sports venues, parks, exhibitions, etc.
Long Range Fiberglass Horn Speakers,waterproof glass fiber horn speaker,Stadium Horn Speaker,full range horn speaker, Fiberglass Horn Speaker
Taixing Minsheng Electronic Co.,Ltd. , https://www.ms-speakers.com